在大型锻件的热处理中,尤其是在粹火过程中,经常会碰到断裂问题,断裂形式有横裂、纵裂、脱肩、置裂、剥落、龟裂等。而其断裂原因是极其复杂的,往往是多种因素作用的结果,但从总的方面来考虑不外是两方面的因素:一是内应力(拉应力)超过材料的实际破断强度,二是虽然内应力并不过高,但由于材料本身的缺陷造成材料强度下降。以下就从这两方面来分析一下大锻件裂纹产生的情况。
(一)横裂
形成横向裂纹时内应力分布的特征是:表面受压应力,离表面一定的距离应力发生剧变,由压应力变为很大的拉应力。裂纹产生在拉应力峰值区域内,然后当内应力重新分布或钢的脆性进一步增加时才蔓延到工件表面。横向裂纹的特点是垂直于轴的方向,这类裂纹往往发生在未淬透的工件中,因为淬硬与未淬硬的过渡区有一个大的应力峰值,而且轴向应力大于切向应力。
大型锻件因不可能全部淬透,而且往往存在较严重的冶金缺陷(如气泡、夹杂、银造裂纹、偏析、白点等),在热处理宠力作用下,以这些缺陷为裂纹的起点,缓慢扩张直到***后突然断裂。另外在轧棍的横断实例中,往往在断裂面上不能看出明显的断裂起点,这像刀切的一样,这是较脆的材料在热应力作用下引起断裂的特征。
对起重机车轮锻件来说,打中心孔并对表面和中心一起冷却,可使拉应力的峰值移向中间层,数值也可大大降低,所以这是防止横断的有效方法之一。然而打中心孔时往往会使冶金缺陷暴露到中心孔表面,亦有其不利之处。
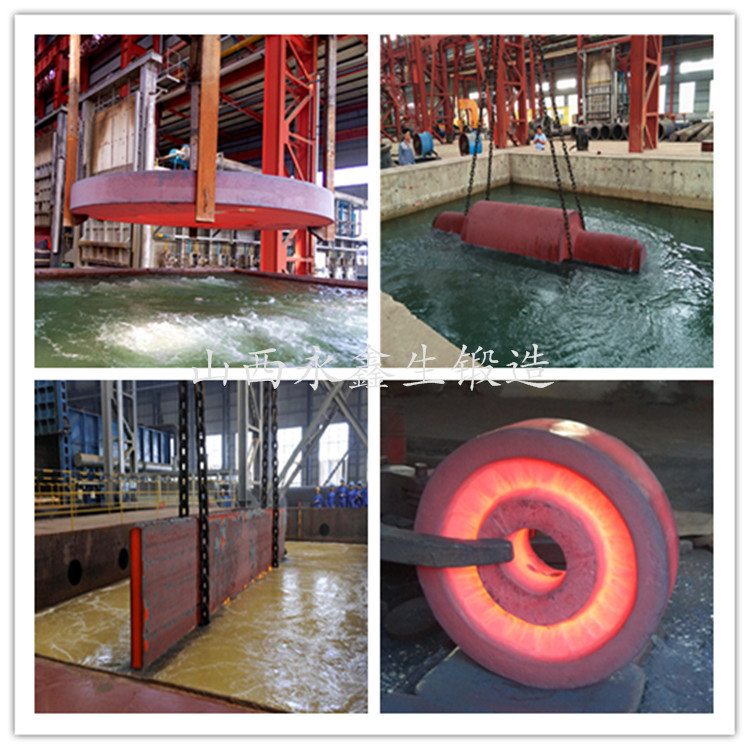
(二)纵裂
裂纹产生于工件表面附近***大拉应力处并裂向心部有较大深度的裂痕,裂纹的走向一般平行于轴向,但是工件存在应力集中部位或内部组织缺陷等,裂纹也可能改变走向,在完全淬透的工件中容易产生纵向裂纹,这与淬透工件的表层存在较大的切向拉应力有关,并且随碳含量的提高,形成纵向裂纹的倾向增大。低碳钢因马氏体比容小,而且热应力作用强,表面存在很大的残余压应力是不易淬裂的。随着碳含量的提高,表面压应力减少(组织应力作用增强),拉应力峰值移向表面,碳含量高的马氏体其破断抗力降低,因此高碳钢在过热的情况下淬裂的倾向增大。
工件尺寸直接影响淬火后残余应力大小和分布,直径小的工件因表层与心部的温差小,淬火时应力也小,故不易淬裂。在淬透的情况下,随着直径增大,一方面悴火后的残余应力值增加,另一方面却由于拉应力峰值逐步远离表面,则有利于阻止表面裂纹的产生。由此看来,对工件淬透的情况下有一个淬裂的敏感尺寸,接近此尺寸的工件有淬裂的危险。实践经验表明,碳素钢淬火时的危险尺寸约为8~15mm,低合金钢油淬的危险尺寸约为25~40mm。
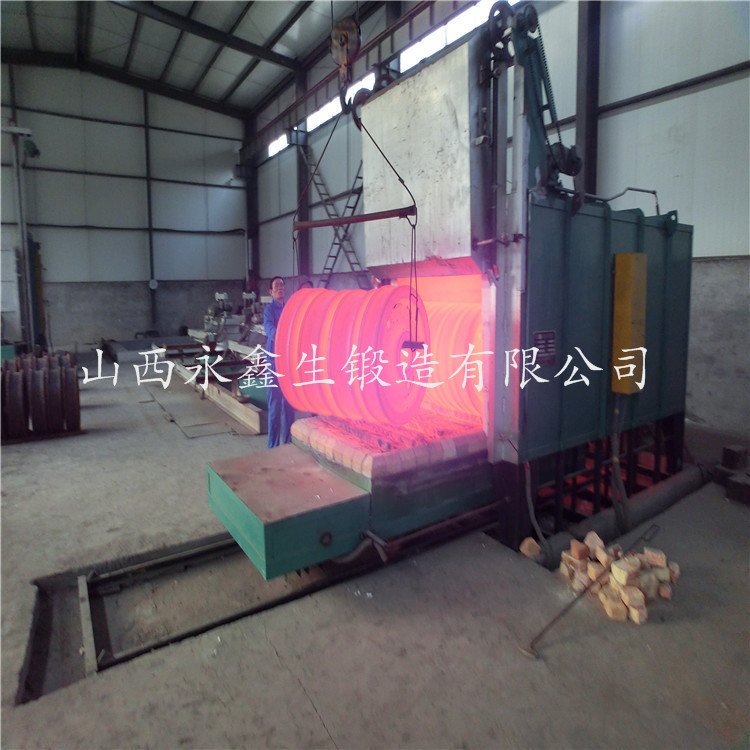
(三)置裂
零件在热处理终了后,在长时间放置中发生自然破断的现象称为置裂。产生置裂的主要原因是内应力与氢气的联合作用和残余奥氏体的分解。
目前在考虑氢和应力的联合作用时,认为氢原子在应力的作用下,将向缺陷***处有应力集中的三向拉应力处聚集,沉淀在位错线上,对位错起钉扎作用,使它不能自由运动,导致材料产生局部硬化。随后在外力或内应力的继续作用下,在局部硬化区产生裂纹并逐渐发展长大。当裂纹长大到贫氢区后,位错线的运动恢复自由,基体可以通过塑性变形使应力松弛,裂纹长大停止。以后随着时间的延长,氢原子在应力的作用下重新在裂纹前沿集结,材料又产生局部硬化,裂纹又继续长大。这一过程不断重复,裂纹一段一段扩大,***后导致突然断裂,由此可见,这种脆断过程是为氢原子在应力作用下的扩散所控制。
当热处理后工件中含有较多的残余奥氏体时,由于残余奥氏体分解,发生体积膨胀和氢的溶解度突然下降,引起了内应力增加和氢脆作用加剧,亦将导致置裂。
防止置裂的方法主要是减小钢中的内应力和氢气含量,使之不至于引起破断。